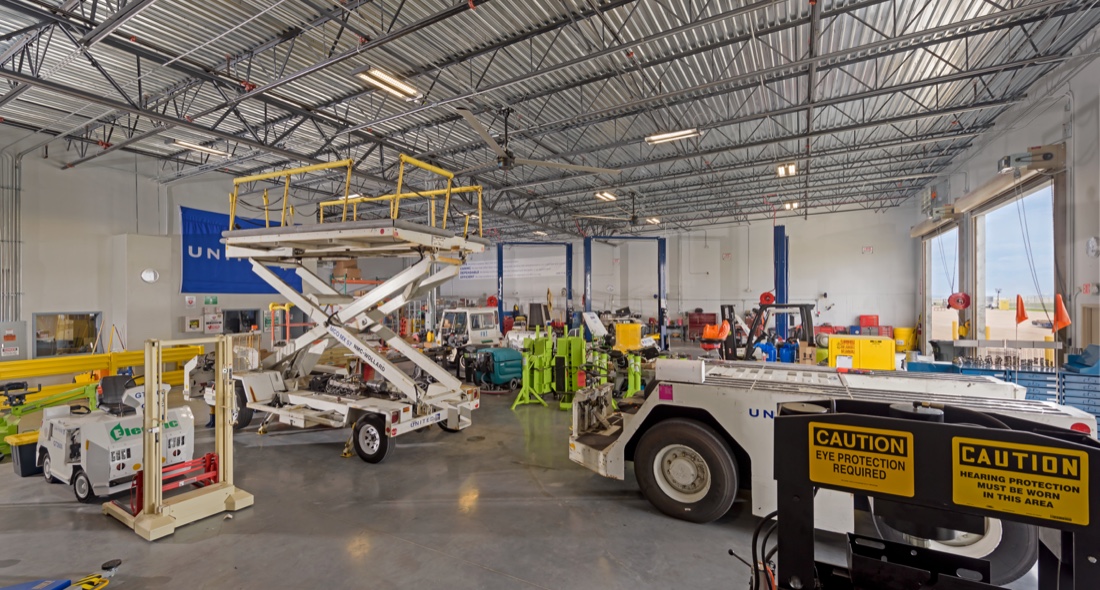
CASE STUDY
Reimagining GSE Maintenance at Orlando Airport
AFCO helped the Orlando International Airport (MCO) recapture valuable apron space by conceiving and delivering an environmentally responsible consolidated GSE facility.
In 2006, ground operations at Orlando International Airport were chaotic and inefficient. Ground service equipment was clogging the apron and the airport lacked any environmentally friendly facilities for oil-water separation or equipment wash bays. Airlines and their maintenance providers wanted relief.
AFCO’s Idea, AFCO’s Risk
Demand for a GSE facility was evident and AFCO responded. Leveraging AFCO’s longstanding relationships with the Greater Orlando Airport Authority (GOAA), our team requested a ground lease and provided our own financing to construct a multi-tenant, streamlined, central GSE facility that would improve efficiency, improve aesthetics and provide much needed space to house environmental supports.
Delivering Success
The concept of a centralized GSE facility was previously reserved for single airlines at major hubs. AFCO delivered a 38,000 square feet, facility at MCO in 2006. This Phase 1 facility was filled within six months, proving the demand for this multi-tenant concept. Phase 2, an additional 40,000 square feet facility, is already half leased since coming on line in the summer of 2018.
Environmental Impact
The success of these multi-tenant ground service equipment facilities is measured in the recaptured apron space that can be put to better use by the airlines, as well as important environmental improvements. Airline maintenance crews now have access to wash bays to eliminate run-off, and oil-water separators that keep waterways clean.
Orlando International Airport is now a model of GSE efficiency and environmental stewardship, with other airports adopting consolidated GSE facilities.